Production planning and control is a research stream concerned with planning for production facilities and the realization of production plans. It is based on a holistic approach, which takes all requirements, dependencies and aspects of production processes into account. The planning aspect encompasses forecasts, material provisions, assignment of human operators and scheduling of production, while the control aspects focuses on monitoring and adjustment of production plans to practice in real time.
Centralized versus Distributed Control
Optimization of manufacturing facilities is not a novel concept, but arguments can be made that the modern research fields starts around the turn of the 20th century. Ever since, they question of optimal decision-making and control design occurred at several times, always questioning the current perception of the field regarding control architecture, oscillating between either fully centralized control approaches with monopolized decision-making authority and completely distributed decision-making authority, enabling any number of entities within production to exhibit autonomy regarding its respective decision space.
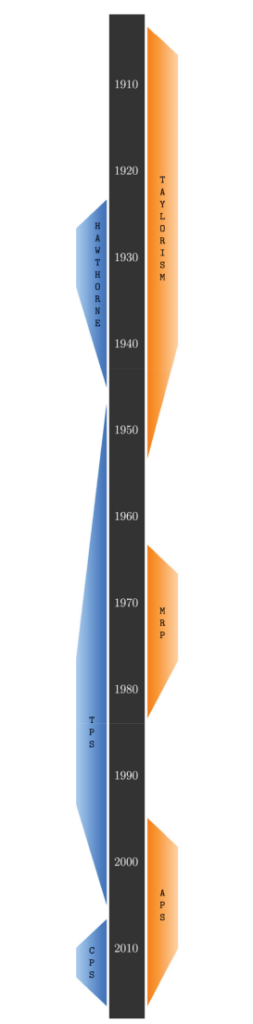
Scientific Management
In the early 20th century a new form of scientific management referred to as Taylorism emerges, named after the American engineer Frederick Taylor. It is based on the strict separation of planning and execution and the idea to split the entire production process into as many as small tasks as possible. Early assembly lines for the Ford model T showcase this concept, with every worker assigned to one specific task of manufacturing.
Hawthorne Experiments
In the early 1920s, studies on worker efficiency show that sufficient pay was not the most efficient motivator for human workers. Rather, the ability to exhibit autonomy within their work was highly valued. This results started intense discussions in management research and practice, influencing ideas like the Exploration versus Exploitation trade-off and the Tavistock approach.
Material Requirements Planning – New Mathematics
With the introduction of first computers to manufacturing planning facilities, first concepts of mathematical planning beyond reorder point and lot size formula emerged. The newly available computation power was utilized to solve linear programs describing the production flow of multiple components and parts, considering both lead times and inventory levels. The most notable example is Material requirements planning (MRP), which centralized control approach was promoted extensively in the 1970s.
Lean Production – Toyota’s Concepts
An increasing number of product variants and endless part variants resulted in highly automated but absolutely rigid an bureaucratic production plans. An entirely different concept was developed in Japan by Toyota, which was the concept for lean production. Contrary to rigid planning systems such as MRP, lean production views the production systems as set of individual cells, which autonomously request material when needed, resulting in a PULL system. The degree of worker responsibility and corresponding decision space can be viewed as degree of autonomous control.
Advanced Planning and Scheduling – MRP II
The continuous increase in computation power and subsequently reduced costs, as well as significant advances in mathematical optimization resulted in a greatly increased solving performance for MILPs in the early 2000s. This performance increased allowed for far more complex models of production systems, allowing the consideration of a multitude of influencing factors and variables. As such, Advanced Planning and Scheduling (APS) emerged as successor of MRP, taking many aspects of supply chains into consideration as well. This approaches argued again for the centralization of all decision-making authority.
Cyber-Physical Systems
Many advancements in microprocessor production allowed for cheaper costs, smaller sizes, less energy consumption as well as increased integration, capabilities and reduced prices. As such, it became feasible to equip every production machine and even products with computation, communication and sensory capacities. While this allows for great insight into production processes through extensive data collection and availability, it also provides the technical requirements for any such entity to act autonomously within a production system.